Maßgeschneiderter Start für Jungunternehmer dank Protoforms Space Puzzle Molding
19.12.2013 / ID: 150807
Maschinenbau
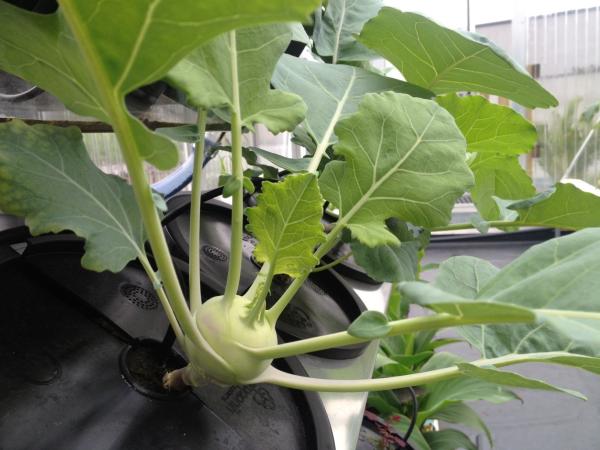
Dass die Systeme zum Gemüseanbau jenseits des Gartens und ohne die industrieübliche Steinwolle nun fix und fertig zum Kauf im Fachhandel stehen, ist dem Fürther Kunststoffspezialisten Protoform mit zu verdanken. Denn Protoform lieferte die ersten Bauteile für die aeroponischen Pflanzgefäße. "Das Außergewöhnliche an Herrn Herings Projekt war, dass er mit einem festen Budget bei uns vorstellig wurde", erinnert sich Wolfgang Tykvart, Geschäftsführer von Protoform, an Markus Herings ersten Besuch in Fürth. Dem erfahrenen Techniker war gleich klar, dass das schmale Budget nicht ausreichen würde, um die Vorstellungen des neuen Kunden zu realisieren. Trotzdem nahmen die Konstrukteure bei Protoform die Arbeit auf. "Wir sind immer sehr aufgeschlossen gegenüber Leuten, die Ideen haben. Wir helfen gerne, innovative Pläne Wirklichkeit werden zu lassen", sagt Wolfgang Tykvart.
Die Entwicklungsabteilung bei Protoform löste das Problem zur Zufriedenheit aller Beteiligten. Das in Auftrag gegebene Zubehör für die aeroponischen Pflanzgefäße - hundert Gitter, um den Wurzeln der Pflanzen im substratlosen Anbau Halt zu geben, und hundert Deckel, um das Aerosol im Pflanzgefäß zu halten - wurden spritzgusstechnisch und im Hinblick auf die Kosten optimiert. Die Konstrukteure modifizierten zudem eines der beiden Bauteile, den Deckel des aeroponischen Pflanzgefäßes, und ließen es in der hauseigenen Spritzerei in einer vereinfachten Variante produzieren. Die fehlenden Features des Deckels ergänzte Markus Hering von Hand.
"Ich war gespannt, ob wir in der Lage sein würden, die Bauteile innerhalb des äußerst knappen Budgets zu produzieren. Aber eigentlich war ich von Anfang an überzeugt, dass es klappen würde", so Wolfgang Tykvart. Protoform verfügt über eine Technologie, die es erlaubt, Kunststoff-Bauteile, die bisher nur als Datensätze existierten, kostengünstig in Serienmaterial und serienidentischer Qualität herzustellen. Space Puzzle Molding (SPM) wurde von Protoform-Gründer Konrad Hofmann in den 1980er-Jahren entwickelt und ist das weltweit schnellste Rapid-Tooling-Verfahren, um komplexe Bauteile im Spritzguss herzustellen.
Das patentierte SPM-Verfahren ist geprägt durch einen minimalistischen Werkzeugaufbau, der die kostengünstige Produktion hochkomplexer Bauteile in kleinsten Serien ermöglicht. Die Aluminiumformen werden möglichst kompakt gehalten und bestehen aus vielen Einzelteilen, die in einem Formrahmen wie ein Puzzle zusammengesetzt werden. Zum Entformen der gespritzten Kunststoffteile wird das Werkzeug von Hand zerlegt. SPM-Formwerkzeuge kommen ohne komplizierte Formschieber, Kühlsysteme und aufwändigen Auswerferkasten aus. Komplexe Konturen und Hinterschneidungen werden schieberlos durch demontierbare, lose eingelegte Formeinsätze realisiert.
Im hauseigenen Werkzeugbau entstehen bei Protoform auf diese Weise innerhalb kürzester Durchlaufzeiten kostengünstige, voll funktionsfähige und gleichzeitig unproblematisch veränderbare Formwerkzeuge. Angusssystem und Angussführung können ohne großen Aufwand optimiert und Formeinsätze ausgetauscht werden. Die Ausbringungsmenge dieser vereinfachten Formwerkzeuge liegt bei 500 bis maximal 3.000 Stück, in Einzelfällen auch höher.
Da im SPM-Verfahren üblicherweise Originalwerkstoff eingesetzt wird, erhält der Auftraggeber auch geringe Stückzahlen bis hin zu Einzelteilen in serienidentischer Qualität. Die Kosten für eine SPM-Form können bis zu 50 Prozent unter den Herstellungskosten für eine konventionelle Spritzgussform liegen. Gleichzeitig erfolgt die Lieferung der benötigten Teile doppelt so schnell, denn Protoform baut in Fürth auf über 3.000 Quadratmetern Produktionsfläche nicht nur die Formen, sondern fertigt in einer modern ausgestatteten hauseigenen Spritzerei mit Baugruppenmontage auch die georderten Bauteile.
Im Falle des Kunden Aeroponik Systems ging es nicht nur darum, kurzfristig Teile zur Verfügung zu stellen, sondern auch um Versuche mit einem bis dato eher selten benutzten Werkstoff. Markus Hering will sich mit einer kompostierbaren Ausstattungsvariante speziell an die Kundengruppe des industriellen Gemüseanbaus wenden. "Bisher verwendet man in diesem Bereich Steinwolle als Substrat. Durch Anwendung des substratlosen aeroponischen Systems können die Produzenten viel Geld sparen", sagt Markus Hering im Hinblick auf die kostenintensive Entsorgung der benutzten Steinwolle-Matten. Wenn Aeroponik zum Einsatz kommen soll, bevorzugen professionelle Anbaubetriebe aus wirtschaftlichen Gründen die Kompostierung des vollständig umwurzelten Trägergitters mit der abgeernteten Pflanzenstaude. Deshalb bietet der Gründer eine Gittervariante aus einem biologisch abbaubaren, nachwachsenden Rohstoff an.
Bei Protoform orderte er zu Versuchszwecken neben Bauteilen aus Polypropylen Borealis BF 970 auch Gitter aus drei unterschiedlichen Bio-Kunststoffen von Tecnaro. Nach dem Abschluss einer anwendungstechnischen Versuchsreihe entschied sich Markus Hering für Arboblend V3 natur. Tecnaro stellt die Biokunststoffe aus Holzabfällen her. Der Werkstoff überzeugte durch gute Haltbarkeit und ein gegenüber den anderen Materialien besseres Schrumpfverhalten. Auch die Kompostierbarkeit wurde im praktischen Versuch erwiesen. Nach einem Jahr war das Gitter komplett biologisch abgebaut. Wolfgang Tykvart kann diese Ergebnisse nur bestätigen. Im Nachhinein führte das Unternehmen selbst Versuche mit dem Bio-Kunststoff durch. "Unser Ziel war es, eigene Erfahrungen mit dem Bio-Werkstoff zu sammeln, auch für andere Anwendungen", sagt Tykvart.
Für Markus Hering hat sich die Entscheidung für Protoform bezahlt gemacht. Bei einem Spritzgussunternehmen gab er inzwischen eine marktreife Serie seines aeroponischen Zubehörs in Auftrag. Die Erkenntnisse von Protoform konnte der Auftragnehmer beim Werkzeugbau und im Produktionsprozess nutzen. "Wir stellen unseren Kunden die Ergebnisse der spritzgusstechnischen Optimierung ebenso wie bei der Herstellung der Teile gesammelte Erfahrungswerte zur Verfügung", sagt Wolfgang Tykvart.
Protoform bietet auch Unterstützung, wenn es darum geht, nach der Kleinserienfertigung in die marktreife Serie oder gar in die Großserie zu gehen. In einem Netzwerkverbund arbeitet das Unternehmen unter anderem mit Spritzgießbetrieben, aber auch mit Veredlern zusammen.
Protoform K. Hofmann GmbH
Herr Wolfgang Tykvart
Siemensstraße 45
90766 Fürth
Deutschland
fon ..: +49 (0)911 7599 170
fax ..: +49 (0)911 7599 100
web ..: http://www.protoform.de
email : wolfgang.tykvart@protoform.de
Pressekontakt
Beate Ziehres
Frau Beate Ziehres
Bardenbike 8
38350 Helmstedt
fon ..: +49 (0) 172 416 7792
web ..: http://www.ziehres.de , http://www.beateziehres.de
email : beate@ziehres.de
Diese Pressemitteilung wurde über Connektar veröffentlicht.
Für den Inhalt der Pressemeldung/News ist allein der Verfasser verantwortlich. Newsfenster.de distanziert sich ausdrücklich von den Inhalten Dritter und macht sich diese nicht zu eigen.
Weitere Artikel in dieser Kategorie
25.07.2025 | SCHENCK RoTec GmbH
Neue Schutzumhausung und Antriebssysteme - Schencks Universalauswuchtmaschine Pasio 100 - 700
Neue Schutzumhausung und Antriebssysteme - Schencks Universalauswuchtmaschine Pasio 100 - 700
24.07.2025 | Merkle CAE Solutions GmbH
Wasserstoff-Innovation in Deutschland
Wasserstoff-Innovation in Deutschland
24.07.2025 | Panasonic Marketing Europe GmbH
PANASONIC AUTOMATISIERT PRODUKTIONSLINIE VON HAELVOET MIT G4-SCHWEISSROBOTERSYSTEM
PANASONIC AUTOMATISIERT PRODUKTIONSLINIE VON HAELVOET MIT G4-SCHWEISSROBOTERSYSTEM
23.07.2025 | FUJI EUROPE CORPORATION GmbH
Investition in die Zukunft: FUJI baut multifunktionales Gebäude in Kelsterbach an
Investition in die Zukunft: FUJI baut multifunktionales Gebäude in Kelsterbach an
22.07.2025 | FLURO®-Gelenklager GmbH
Hersteller von Gelenklager
Hersteller von Gelenklager
